Trickle and Roll Dip Impregnation Machine
Trickle and Roll Dip Impregnation Machine improves the varnishing quality coupled with reduced cost. The varnishing technique used in this machine is now well accepted and used for impregnating stators, fields and armatures, rotors etc. We are one of the prominent Manufacturers and Suppliers of Trickle and Roll Dip Impregnation Machine. We supply Trickle and Roll Dip Impregnation Machine only after the completion of testing procedures.
Trickle Impregnation Technique :
According to the principle of Trickle Impregnation, activated resin is trickled in a thin jet on to the rotating preheated winding. The resin immediately gets heated and its viscosity is reduced. Due to the rotary motion of the winding the resin gets distributed evenly inside the winding without any drain loss. The heated winding accelerates the gelling and curing of the resin.
The resin applied on the winding is quickly sucked through the slots. Assisted by the capillary action it pushes out the trapped air from the small voids and gaps in the winding and penetrates evenly in all the voids.
The essential point for successful application of the trickle impregnating resin is the correct adjustment and the control of the winding temperature.
Design of a trickle Impregnation Plant :
The design of a trickle Impregnation Plant plays a vital role in ensuring the uniform quality of a trickle impregnation. Any trickle impregnation plant should have the following essential features.
Automated Cycle, independent of operator.
* Arrangement for quick mounting and for making the connections of resistance heating.
* Precise temperature control of the winding.
* Accurately metered resin quantity required for the component.
The trickle impregnation plants with the above features are custom built taking into account several factors such as production rate, size and shape of the component, type of trickle resin etc.
Mainly three types of trickle impregnation plants are popular for various types of components.
* Multi Spindle Trickle Impregnation plant. (Batch type) : It is ideal for stators of A. C. motors. Depending on the production rate the quantity of the spindles can be decided.
* Multi Spindle Rotary Indexing Type Trickle Plant : It is ideal for medium size stators and rotors e.g. armature and field coils of hand tools, auto electrical, household appliances etc. High production rates of 60 to 120 jobs per hour are possible with these plants.
* Conveyorised Trickle Impregnation Plant : This plant is similar to that of indexing type. However a chain conveyor carries the components instead of indexing movement. This plant is especially suitable for large output of impregnated small and medium sized components. Generally this plant is installed in a conveyor production line of components.
* Advantages of Trickle Impregnation : Trickle impregnation process is especially characterized by its low energy cost due to a very short cycle time compared to Dip varnishing or the Vacuum impregnation. Compared to the Dip and bake varnishing method, which uses varnishes containing 50 to 55% solvents and the impregnation cycle of 8 hrs to 24 hrs. Trickle impregnation cycle times are substantially low to the tune of 20 min. to 40 min. Hence it is quite evident that trickle impregnation process offers the most cost economical answer to the impregnation process.
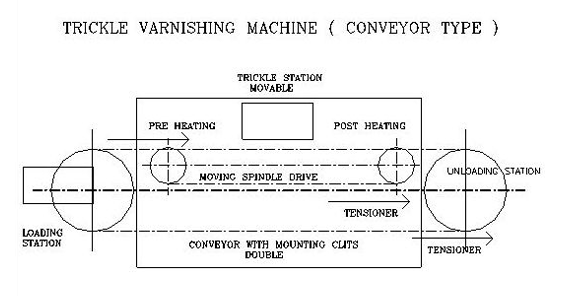
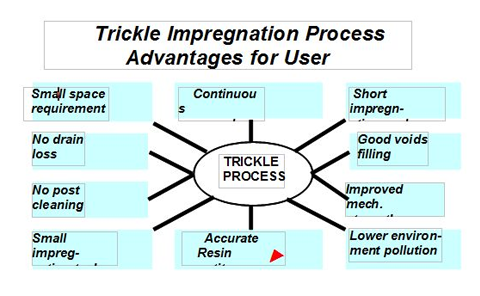